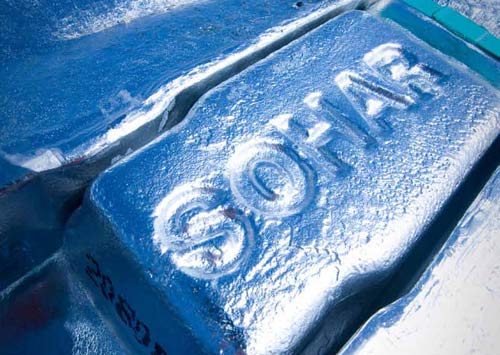
Like its neighbours Oman developed its economy on oil and gas, and like them it is now trying to diversify that economy by establishing industries that will sustain its growth over decades to come. Oman occupies a favourable position on the east coast of the Arabian desert peninsula so in 2004, with the strategically placed Port of Sohar designated as a major industrial hub it made sense to set up an aluminium smelting operation there.
Being a heavy consumer of electricity, aluminium smelting is in the process of moving away from the industrial nations of the West where energy is relatively expensive, to the Middle East and other countries where power is cheap. With a ready supply of gas that would previously have been flared off from the oil wells, many of the oil producing countries are capable of generating large amounts of power at a relatively low cost, and this is ideal for the power hungry smelting process.
Sohar Aluminium was established in 2004 as a flagship enterprise on the Sohar site. It has three shareholders, the government-owned Oman Oil Company and TAQA, a subsidiary of Abu Dhabi Water and Electricity Authority, holding 40 percent each and Rio Tinto Alcan the remaining 20 percent. The plant currently produces 375,000 tonnes of aluminium per annum, and employs a workforce of 1,000 people, though CEO Henk Pauw estimates that it supports around 3,000 jobs in the Sultanate if downstream industries are taken into consideration.
One such business, a $388 million aluminium rolling mill is currently under construction and expected to come on stream in August 2013. “Our target is to pass 60 percent of our output on to Omani companies,” says Pauw. “We’re not there yet, and there’s still room for improvement. But once the rolling mill is up and running we will be getting close to that target.” Another nearby factory takes a proportion of the output for high voltage cables. By manufacturing from liquid aluminium direct from the smelter, the cable factory is able to operate at competitive cost, bypassing the metal melting process most of its competitors go through.
The smelting plant itself is powered by a 1,000 MW combined-cycle captive power generation facility (CCPP) designed and built by Alstom and owned by Sohar Aluminium, which produces abundant low cost energy fuelled by natural gas that is supplied under the terms of an agreement with the government of Oman. The generation facility consists of two blocks, each with two Alstom GTI 3E2 gas turbines exhausting to a heat recovery steam generator with a common steam turbine
The availability of cheap fuel and low labour costs do not mean that the plant can ignore world-class process standards or the need to conserve energy. Drawing on his ten years’ experience in the automotive industry Pauw introduced lean practices at the plant and has been developing them through training, encouraging a mindset of empowerment and responsibility among employees. “The principles are always the same,” he says. “Lean is about focusing on waste and empowering people on the shop floor. It’s about toolboxes and data, about taking responsibility and doing something about it—not blaming other people.”
The Sohar Aluminium Academy based at the plant provides a comprehensive programme of training, from welding and technical courses through to safety, management and leadership training. “We started our first lean workshops about two years ago and have been rolling it out over different departments. Most of our leaders have completed a three-day lean session where they have learned about the principles of lean and about the lean toolbox.”
Sohar Aluminium is something of a pioneer for lean in Oman. Sohar Aluminium being a new business built from scratch it had the opportunity to introduce lean thinking from ground level among its employees, many of them new to working in industry. Coming from a society that values authority Omanis are sometimes slow to realise that the opinion of a shop floor worker is as valued in a lean environment as that of senior managers. “With lean, we are turning the traditional hierarchical management pyramid on its head and creating a serving leadership and not a boss leadership.”
Looking to the future, Pauw’s objectives go well beyond achieving the expansion project. Good management has kept the plant self sufficient in terms of finance, and he is determined it will stay in the black, offsetting any straitening in global markets by cost reduction and continuous improvement – lean manufacturing is a never-ending process. His targets are by no means limited to things that can be demonstrated on the balance sheet. “We want to create future leaders for Oman. We believe we have a job training role to play, and I would like to see some of our Sohar Aluminium employees find jobs in other companies and to be recognised as the best employees to have.”
And these principles extend beyond the direct workforce. Last year Oman's Public Authority for Craft Industries (PACI) has signed a memorandum of understanding with Sohar Aluminium to set up a training centre for aluminium craft work on the company's premises. The two-year training programme aims to enable women to become entrepreneurs and produce aluminium handicrafts. According to the agreement, PACI will provide trainers and study material while Sohar Aluminium will provide the faculties and funding for the programme, while the centre will train selected women from low-income families in the local community in aluminium craft manufacturing.
So what of the future? Following an extensive study on future demand locally and internationally Sohar Aluminium is planning to invest around $4 billion to ramp up the capacity of its plant to 1 million tonnes a year. Following weak prices in 2012, global aluminium is showing a positive trend in early 2013, with good potential for growth. “There’s a need for two or three new aluminium smelters a year globally just to keep up with demand,” estimates Henk Pauw.
The Sohar plant has a big advantage in is its access to Alcan’s cutting edge technology, the most reliable and consistent on the market today: it was the first smelter in the world to implement Rio Tinto Alcan's benchmark AP36 smelting technology. Alcan is constantly improving the efficiency of its equipment, and any future expansion will look at incorporating the latest AP 40 technology, with its associated benefits of energy saving and emission reduction. “If ongoing talks with the Ministry of Oil and Gas are positive the company would definitely like to undertake this expansion to triple the capacity of the plant.”
Written by John O’Hanlon, research by Robbie Hodgson